Why South Florida’s Coastal Demolition Projects Demand Specialized Expertise
- content255
- 5 days ago
- 6 min read
Navigating the Complexities of Beachfront and Water-Adjacent Demolition
Hook: "A single misstep in coastal demolition can send tons of debris cascading into protected wetlands—or worse, the Atlantic Ocean. In South Florida, where environmental regulations are stringent and conditions unforgiving, standard demolition methods simply won’t cut it."
Problem Statement: Traditional demolition techniques are ill-equipped to handle South Florida’s unique coastal challenges, including saltwater corrosion, high water tables, hurricane-resistant construction, fragile ecosystems, and restricted site access. Contractors who fail to recognize these differences risk catastrophic project failures, massive fines, and irreversible environmental damage.
The Solution: Only demolition specialists with extensive experience in marine-sensitive demolition can navigate these complexities safely, efficiently, and in compliance with strict regulations.
Preview: This in-depth guide explores the five critical factors that set coastal demolition apart—and why hiring a contractor with specialized expertise isn’t just recommended, but absolutely essential.
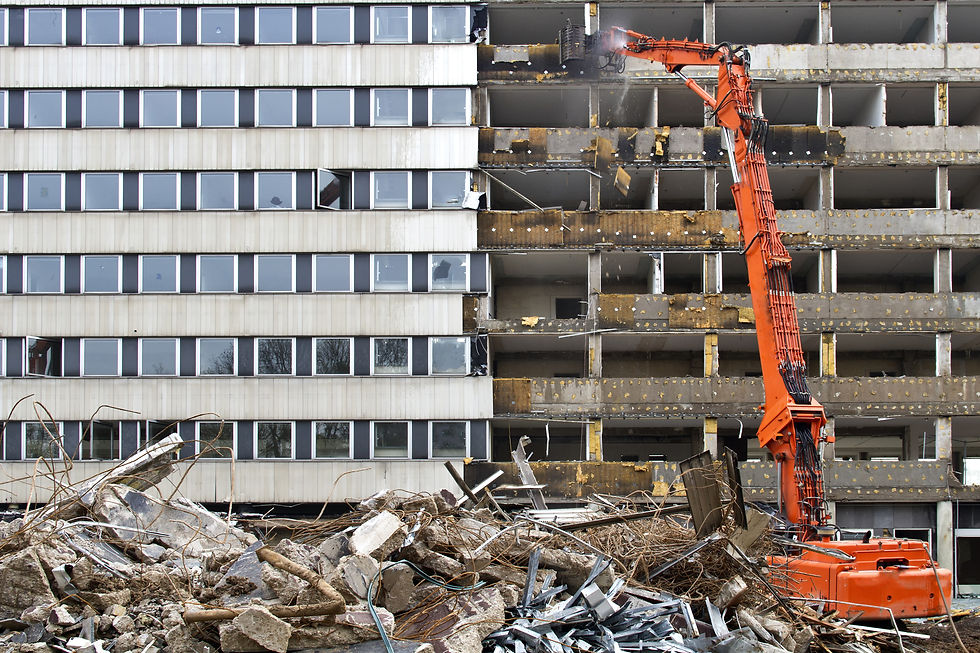
1. The Saltwater Factor: Corrosion and Structural Instability
The Science Behind Saltwater Damage
Coastal structures endure relentless exposure to salt spray, high humidity, and storm-driven seawater, leading to accelerated metal fatigue and concrete spalling. Research from the Florida Department of Environmental Protection (FDEP) indicates that steel reinforcements in coastal buildings degrade 30-50% faster than those inland. This hidden corrosion weakens structural integrity, turning what appears to be a stable building into a demolition hazard.
Specialized Equipment & Techniques Required
Rust-resistant machinery: Standard excavators and bulldozers corrode rapidly in salty air, leading to equipment failure. Marine-grade hydraulic systems and stainless-steel components are mandatory.
Precision dismantling over wrecking balls: Uncontrolled collapses risk debris entering waterways, violating DERP (Derelict Equipment Removal Program) regulations.
Advanced scanning technology: Ground-penetrating radar (GPR) and ultrasonic testing detect hidden corrosion before demolition begins.
Case Study: The Sunny Isles Fishing Pier Demolition (2021)
When demolishing this 40-year-old pier, engineers discovered severe pitting corrosion in support beams that initial inspections missed. A traditional wrecking ball approach could have caused a catastrophic collapse, South Florida demolition sending tons of concrete into the ocean. Instead, the team used:
✔ Hydro-process cutting to segment the pier systematically
✔ Barge-mounted cranes to lift debris without shoreline disruption
✔ Real-time environmental monitoring to prevent marine contamination
Result: Zero environmental violations, completed two weeks ahead of schedule.
2. High Water Tables: South Florida’s Invisible Demolition Challenge
Why Miami’s Geology Makes Demolition Different
Over 80% of coastal Miami-Dade County sits on porous limestone bedrock, creating a high water table that complicates excavation and foundation removal. When improperly managed, demolition can:
Trigger saltwater intrusion into freshwater aquifers (a violation of South Florida Water Management District (SFWMD) rules)
Cause sudden site flooding, endangering workers and equipment
Destabilize adjacent structures through subsidence
Proven Dewatering Strategies for Coastal Demolition
Well point Systems: A series of shallow wells pumps groundwater away from the excavation zone.
Cofferdams: Temporary watertight enclosures allow dry demolition in submerged areas.
Electro-osmosis: An advanced technique using electric currents to draw water away from soil.
Real-World Example: South Beach High-Rise Basement Removal (2023)
A developer needed to demolish a 1970s-era basement in a high-water-table zone. Standard excavation would have flooded the site within hours. The solution?
✔ A layered dewatering system combining well points and sheet piles
✔ Continuous water quality testing to ensure no aquifer contamination
✔ Slurry walls to prevent lateral water seepage
Outcome: Project completed without flooding or regulatory issues.
3. Hurricane-Resistant Structures: Built to Withstand Storms—And Demolition
Why Hurricane-Proofing Makes Demolition Harder
Post-Andrew building codes require coastal structures to resist Category 5 winds (157+ mph), meaning:
Reinforced concrete with 40% more rebar density than standard construction
Impact-resistant windows laminated with polycarbonate layers
Continuous load paths with steel tie-downs every 4 feet
Specialized Dismantling Techniques
Material | Challenge | Solution |
Reinforced Concrete | Diamond-tipped saws required | Wire saws with seawater lubrication |
Hurricane Windows | Risk of glass shard projectiles | Thermal cutting to soften laminate |
Steel Tie-Downs | Torch-cutting creates fire hazards | Hydraulic shears or plasma cutters |
Cost of Getting It Wrong: A Miami Contractor’s $1.2M Mistake
In 2022, a demolition firm attempted to implode a hurricane-resistant condo using standard explosives. The reinforced structure failed to collapse fully, leaving a dangerously unstable partial shell. The resulting emergency demolition and EPA fines totaled over $1.2 million.
4. Environmental Compliance: Avoiding Six-Figure Fines in Fragile Ecosystems
South Florida’s Unique Environmental Protections
Regulation | Key Requirement | Penalty for Violation |
DERP | 0% debris in waterways | $50,000/day |
Mangrove Protection Act | No removal without permit | $250,000 + restoration costs |
Sea Turtle Conservation | No work during nesting season | $100,000 per disturbed nest |
Best Practices for Eco-Safe Demolition
Triple-Containment Systems: Sediment curtains, turbidity barriers, and vacuum dredging
Wildlife Monitors: Biologists on-site to relocate protected species
Real-Time Water Quality Sensors: Instant alerts if pH/turbidity levels spike
5. The Logistics of Limited Access: Barges, Turtles, and Narrow Streets
3 Unique Coastal Access Challenges
Weight-Restricted Bridges: Many coastal roads can’t support 50-ton excavators Solution: Modular equipment assembly on-site
Turtle Nesting Season (April 1–Oct 31): No heavy machinery on beaches Solution: Winter-only demolition scheduling
Zero-Land-Access Properties: Some sites only reachable by water Solution: Barge-mounted demolition rigs
FAQ
1. Why is coastal demolition more complex than standard demolition?
Coastal demolition requires specialized expertise due to saltwater corrosion, high water tables, hurricane-resistant materials, environmental regulations, and limited access. Standard demolition methods can lead to environmental fines, structural hazards, and project delays. Contractors must use marine-grade equipment, advanced dewatering systems, and eco-friendly techniques to comply with strict South Florida regulations.
2. How does saltwater corrosion impact demolition?
Saltwater accelerates metal fatigue by 30-50%, weakening structural integrity in ways that aren’t always visible. Hidden corrosion can cause unexpected collapses during demolition. Specialized rust-resistant machinery, ultrasonic testing, and controlled dismantling are required to prevent debris from entering waterways and ensure worker safety.
3. What are the biggest risks of high water tables in demolition?
South Florida’s porous limestone bedrock means 80% of coastal sites have high water tables, increasing risks of:
Sudden flooding during excavation
Saltwater intrusion into freshwater aquifers (violating SFWMD rules)
Structural instability from shifting groundwaterProper dewatering systems (wellpoints, cofferdams) are essential to keep sites safe and dry.
4. Why are hurricane-resistant buildings harder to demolish?
Structures built to withstand Category 5 winds use:
Extra-thick reinforced concrete (requiring diamond wire saws)
Impact-resistant windows (needing thermal cutting)
Steel tie-downs every 4 feet (demanding hydraulic shears)Standard wrecking balls or explosives often fail to fully collapse these buildings, creating dangerous debris hazards.
5. What environmental regulations apply to coastal demolition?
Key regulations include:
DERP (Derelict Equipment Removal Program) – Zero debris in waterways
Mangrove Protection Act – No removal without permits
Sea Turtle Conservation – No work during nesting season (April-Oct)Violations can result in fines up to $250,000 and mandatory restoration costs.
6. How do you prevent demolition debris from polluting the ocean?
We use triple-containment systems:
Sediment curtains to trap floating debris
Turbidity barriers to prevent silt dispersion
Vacuum dredging for underwater cleanupPlus, real-time water monitoring ensures compliance with EPA and FWC standards.
7. What are the biggest logistical challenges in coastal demolition?
Narrow beach roads can’t support heavy equipment
Weight-restricted bridges limit machinery transport
Turtle nesting season bans beach work for 6 monthsSolutions include barge-based demolition, modular equipment, and off-season scheduling.
8. Can you demolish a building with no land access?
Yes, barge-mounted demolition rigs can dismantle structures only reachable by water. We’ve used barges for:
Decaying piers
Waterfront condos with collapsed seawalls
Storm-damaged docks
9. How long does a coastal demolition project typically take?
Timelines vary based on:
Size of structure (small pier = 2 weeks, high-rise = 3+ months)
Environmental restrictions (nesting season delays)
Weather conditions (hurricane season halts work)Proper planning can reduce delays by 30-50%.
10. Why hire a specialist instead of a general demolition contractor?
General contractors often underestimate coastal risks, leading to:
Costly fines for environmental violations
Dangerous structural failures from hidden corrosion
Project shutdowns due to improper permitting Specialists like Atlas Industries Inc have 20+ years of permitted coastal demolitions with zero violations.
Conclusion: Why Coastal Demolition is a Discipline, Not a Side Job
Attempting coastal demolition without specialized expertise is a gamble with six-figure consequences. Between hidden corrosion, hurricane-proof materials, and razor-thin regulatory margins, the risks far outweigh any perceived cost savings.
Don’t risk your project—partner with true coastal demolition experts.
📞 Call Atlas Industries Inc today for a free coastal demolition assessment.🌐 Visit https://www.atlasindustriesinc.com/get-a-quote to see our permitted beachfront demolition projects.
Comments